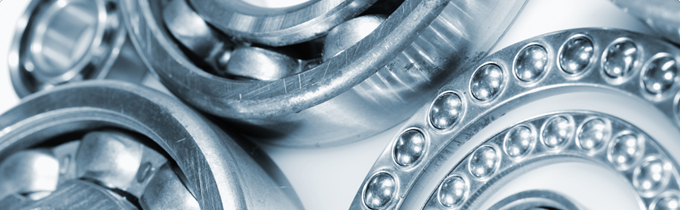
The problem
The majority of paper mills use synthetic or 320-second viscosity lubricating oil in drying line cylinder bearings. These lines run at elevated temperature to dry the paper. The rolls run at high rotating speed on substantial bearings. Once heated to operating temperature, oil is fed to bearings by circulating in a pressurised circuit. Due to the heat, oil may carbonise in bearings and pipe work reducing efficiency in the lubrication system and introducing potentially hazardous abrasive particles into the system.
The solution
One paper mill addressed these problems through the novel use of lighter viscosity 100-second oil treated with a friction inhibitor - Lofrix®.
The system containing 100-second oil originally ran with no additives and showed evidence of progressive restriction and bearing damage. When Lofrix® was added, carbon deposits were released from the pipe work and bearings. Once cleared out, regular oil analysis showed that oil quality was being maintained over a considerable time scale (and without enhanced copper content).
The result
Depending upon system integrity, (i.e. avoiding cooling water leaks) it is possible to achieve an oil change interval of up to 12 months. All 51 cylinders have run for more than 10 years without bearing replacements.
The system never requires oil preheat, leading to immediate start up after stoppages. Reduced maintenance costs, extended bearing life and improved oil life together significantly enhance the productivity of this continuous process.
This paper/board mill now uses a comprehensive range of Lofrix® products, reducing maintenance to a few days a year - whilst production has increased almost fourfold.
ALL CASE STUDIES