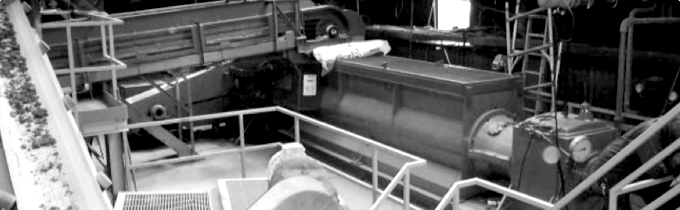
The problem
Energy and environmental costs in the brick making industry are escalating hugely. An opportunity to positively affect maintenance and service costs was considered valuable by one of the, already, most efficient manufacturers. A 500hp motor driven clay extruder gearbox had been in service for several years with rebuild intervals of approximately 7 years. During the interim the first input pinion gear is subject to replacement at 12 – 24 month intervals. Start up is helped by an air bag to cushion the otherwise full load onto clay filled screw. Gearbox oil is changed at 18-month intervals.
The solution
During the most recent gearbox rebuild, which involved replacing approximately £40,000 worth of components, an addition of Lofrix® was made to the new oil fill.
The result
Compared with average power consumption prior to the rebuild, power consumption was reduced by more than 5%.
When the oil was changed at 18 months, the magnetic plug in the gearbox was found to be free from steel or iron particles.
Both at that time and again at two years the input pinion was found to be completely free of damage, thus avoiding a costly stoppage.
All 3 gearboxes on the extruder been treated resulting in significant financial savings being made in both running and maintenance cost.